
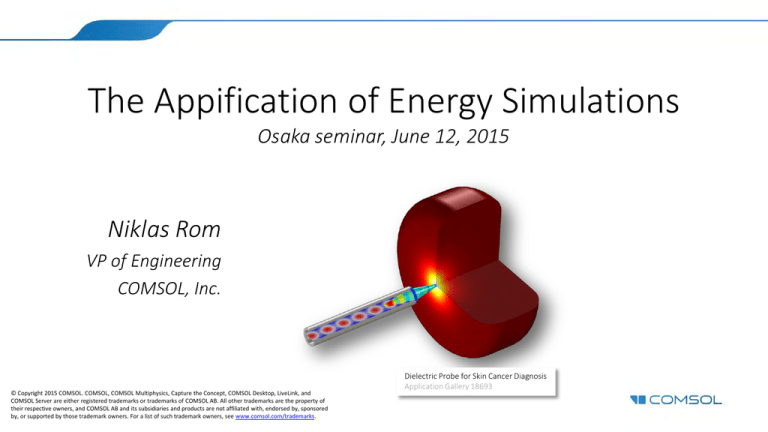
In reality, there are of course no perfectly sharp edges. Numerically, it will tend toward infinity as you refine the mesh. While the electric potential itself remains smooth and well-defined at a sharp corner, its gradient is in theory infinite. The current density is proportional to the electric field, which in turn is (the negative of) the gradient of the electric potential. What you have run into is a geometrically singular result. Singular current density at the inside corner (left) and calculated maximum current density vs. The graph below shows the (quite alarming) results: Even if you refine the mesh by a factor of 100, the maximum current density is still growing and there is no indication that it will ever stop. It is clear that this value appears at the inside corner of the bend, so this time you take care to refine the mesh within that area. The normal mesh gives you a maximum current density of 6.2 A/mm 2. If it is, the resulting heat production risks wearing out the protective jacket and can even be a potential fire hazard. It is important that this value isn’t too high. Next, you evaluate the maximum current density in the wire. Wire model setup (left) and computed electric potential distribution in mV (right).

You judge that the result is mesh convergent and sufficiently accurate for your needs. The results vary only by a few mA and there is markedly less variation between the finer mesh cases. You decide to try a few other mesh settings in order to determine the accuracy of this current.
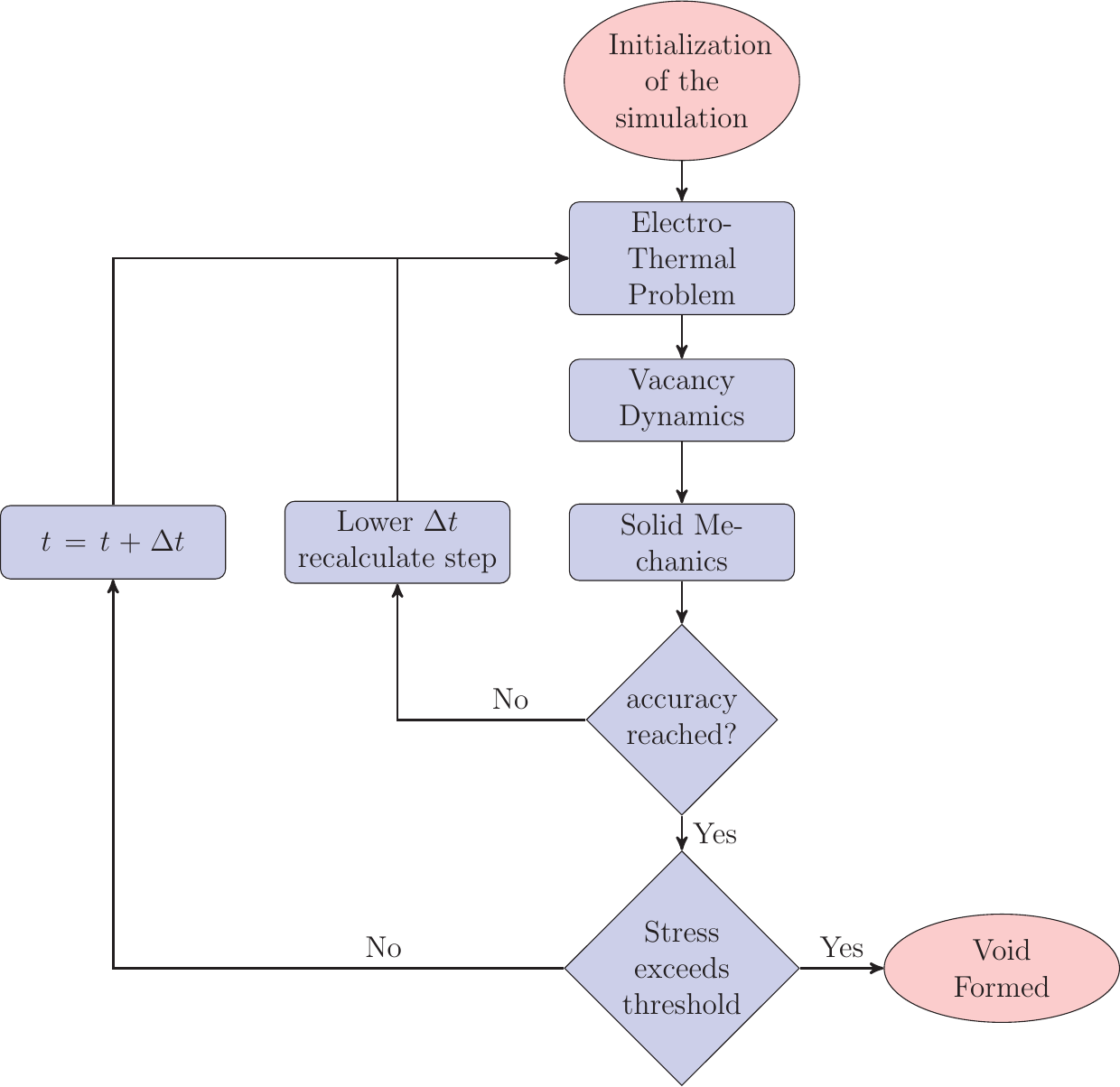
With the default Normal mesh, you get a current of 490 A.

You have applied a voltage of 5 mV between its ends, and the model computes the resulting total current running through it. Let’s look at a model of a bent copper wire. Singular Electromagnetic Fields at Sharp Edges Is this a problem? If so, what can you do about it? Read on to find out. For core materials with positive magnetostriction coefficient the coercive field increases at the increase of dc current intensity passed through the system.No matter how much you refine the mesh at that corner in your geometry, the electromagnetic field that you are computing never seems to settle on a converged value. The magnetic state of the core is influenced by the temperature field induced by a dc current applied to the system. The magnetic behavior of the nanowire was analyzed using the Micromag application. The temperature and stress depend on the size parameters of the system, dc Joule current and the initial temperature of the system. The stresses determined by thermal gradients and different expansion characteristics of core and shell materials were computed. Spatial and temporal evolution of the temperature in system was analyzed using a model based on time-dependent heat conduction equation. An electrical current that passes through the wire induces a temperature and a thermal stress field in the system. The paper analyzes the temperature dependence of hysteretic process in a core–shell nanowire subjected to a dc Joule heating process. Temperature field is an important parameter to be known and controlled in the magnetization process of the core–shell nanowires.
